Smart Manufacturing: Industry 4.0 and Connected Factories
- Date: 07-Jun-2024
- Author: Glamoroxe
- Technology
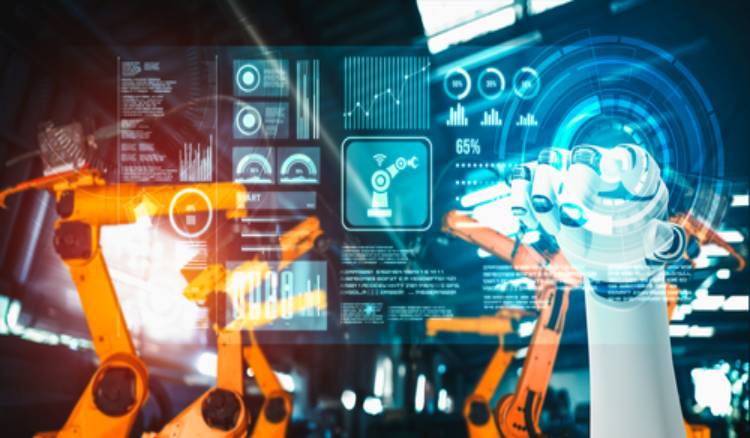
Welcome to the dawn of a new industrial revolution - Industry 4.0, where smart manufacturing and connected factories are no longer futuristic concepts but today's reality. This incredible fusion of physical production with digital technology is transforming not just how products are made, but also how businesses operate in the global landscape. As we delve deeper into this fascinating world, you'll discover how advanced automation, data exchange and cutting-edge technologies such as IoT (Internet of Things), AI (Artificial Intelligence) and M2M(Machine-to-Machine) communication are heralding an era of unprecedented efficiency and productivity in manufacturing processes. With insights from leading industry experts, our post titled "Smart Manufacturing: Industry 4.0 and Connected Factories" provides a comprehensive understanding of the groundbreaking transformation underway within industries across sectors globally.
Understanding the Concept of Industry 4.0
Industry 4.0 refers to the integration of advanced technologies into manufacturing processes, with the aim of creating smart factories that are highly automated, connected, and efficient. This concept encompasses a range of technologies such as the Internet of Things (IoT), artificial intelligence (AI), big data analytics, cloud computing, and robotics. By leveraging these technologies, manufacturers can achieve real-time data collection and analysis, predictive maintenance, enhanced productivity, and improved decision-making. Industry 4.0 enables seamless communication and collaboration between machines, products, and people, leading to increased flexibility, customization, and responsiveness in manufacturing operations. With the ability to connect various aspects of production processes and supply chains, Industry 4.0 has the potential to revolutionize the way factories operate and pave the way for a new era of smart manufacturing.
Exploring the Core Characteristics of Smart Manufacturin
Smart manufacturing, also known as Industry 4.0, represents the convergence of digital technologies and manufacturing processes to create a connected and intelligent ecosystem. At its core, smart manufacturing relies on a set of key characteristics that drive its effectiveness. Firstly, it embraces advanced automation, utilizing technologies such as robotics and artificial intelligence to optimize production processes and enhance productivity. Secondly, it promotes connectivity across the entire manufacturing value chain, enabling seamless communication and data exchange between machines, systems, and stakeholders. Thirdly, it leverages big data analytics and predictive algorithms to enable real-time monitoring, analysis, and decision-making. Additionally, smart manufacturing emphasizes flexibility and customization, empowering manufacturers to quickly adapt to changing demands and preferences. Lastly, it prioritizes the integration of sustainability principles into every aspect of the manufacturing process, promoting resource efficiency and environmental responsibility. These core characteristics collectively form the foundation of smart manufacturing, revolutionizing traditional factories into connected and efficient hubs of innovation.
The Role of Internet of Things (IoT) in Connected Factories
The Internet of Things (IoT) plays a pivotal role in connected factories, enabling a new wave of smart manufacturing known as Industry 4.0. IoT devices, equipped with sensors and actuators, gather real-time data from machines, processes, and products on the factory floor. This data is then transmitted and analyzed in the cloud, providing valuable insights to improve production processes, enhance efficiency, and reduce costs. IoT also enables the seamless integration of information technology with operational technology, allowing for real-time monitoring and control of various manufacturing aspects. Connected factories leverage IoT technologies to enable predictive maintenance, optimize supply chain management, and enhance overall productivity. With the ability to connect and communicate with one another, IoT devices transform traditional factories into intelligent and interconnected systems, revolutionizing the manufacturing industry.
Benefits and Challenges Associated with Smart Manufacturing
Smart manufacturing, also known as Industry 4.0, offers numerous benefits and challenges for businesses in the manufacturing industry. One of the key advantages is increased efficiency and productivity. Through the use of advanced technologies such as the Internet of Things (IoT), artificial intelligence (AI), and data analytics, manufacturers can optimize their production processes, reduce downtime, and enhance overall operational effectiveness. Furthermore, smart manufacturing enables real-time monitoring and predictive maintenance, leading to cost savings and improved product quality. However, implementing smart manufacturing also comes with several challenges. These include the need for substantial investment in technology infrastructure and skilled workforce, as well as concerns regarding data security and privacy. Additionally, the transition from traditional manufacturing practices to smart manufacturing requires careful planning and adaptation to ensure seamless integration of new technologies into existing operations.
Case Studies: Successful Implementation of Industry 4.0 Concepts
Several case studies have demonstrated the successful implementation of Industry 4.0 concepts in various manufacturing industries. For example, Siemens transformed its Amberg Electronics Plant into a smart factory, enabling automation and real-time data analysis across the production processes. This resulted in a 99.99885% product quality rate, a 30% reduction in time to market, and a 75% increase in productivity. In another case, Bosch Rexroth implemented Industry 4.0 solutions in its hydraulic assembly plant, leading to a 50% reduction in assembly time and a 40% increase in productivity. These success stories highlight how embracing digital technologies and implementing connected factories can significantly improve operational efficiency, cost-effectiveness, and overall productivity in the manufacturing sector.