The Role of 3D Printing in Product Design and Manufacturing
- Date: 08-Aug-2024
- Author: Glamoroxe
- Technology
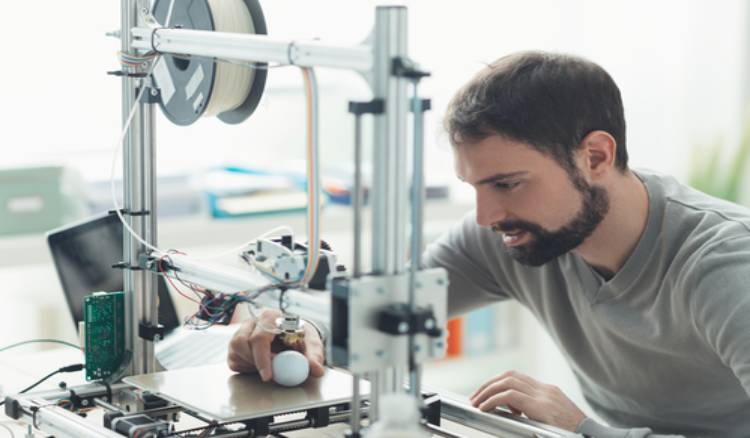
The revolution of 3D printing is transforming the world of product design and manufacturing in ways that were unimaginable a couple of decades ago. This exciting technology has opened up new dimensions, literally, enabling us to print objects layer-by-layer from digital blueprints. The post titled "The Role of 3D Printing in Product Design and Manufacturing" aims to dive deep into this captivating topic. It will explore how this transformative technology accelerates innovation by turning imagination into reality through rapid prototyping and customization. Furthermore, we'll delve into its potential for reshaping production strategies by cutting costs, reducing waste, increasing efficiency and allowing on-demand production. Whether you're an industry professional looking to stay ahead of the curve or simply a tech enthusiast eager about futuristic technologies - prepare yourself for an enlightening journey through one of the most disruptive advancements transforming industries today!
Understanding the Basics of 3D Printing
3D printing, also known as additive manufacturing, is a revolutionary technology that has transformed the way products are designed and manufactured. In this process, three-dimensional objects are created by adding layer upon layer of material, typically plastic or metal, until the desired shape is achieved. The process begins with a digital design file that is sliced into numerous cross-sectional layers. These layers are then printed one by one, starting from the bottom and gradually building upwards. With 3D printing, complex geometries and intricate designs can be created with ease, allowing for unprecedented levels of customization and innovation. This technology offers numerous benefits, including reduced costs, shorter lead times, and increased design flexibility. As 3D printing continues to evolve, it is shaping the future of product design and manufacturing across a wide range of industries.
The Impact of 3D Printing on Product Design
The impact of 3D printing on product design has been transformative. With the ability to quickly and easily create physical prototypes and iterate on designs, 3D printing has revolutionized the product development process. Traditional manufacturing methods often involve complex and time-consuming processes, making it difficult to test and refine designs before mass production. However, with 3D printing, designers can now rapidly prototype their ideas, enabling them to make informed design decisions earlier in the process. This not only speeds up the development cycle but also reduces costs associated with creating physical prototypes. Furthermore, 3D printing allows for greater design freedom, enabling the creation of complex geometries that would be challenging or impossible to produce using traditional manufacturing techniques. Overall, 3D printing has opened up new possibilities in product design, allowing for more innovation and efficiency.
Evolution in Manufacturing with 3D Printing
The advent of 3D printing has revolutionized the manufacturing industry, offering a host of benefits that were previously unimaginable. This technology enables manufacturers to create physical objects from digital designs, eliminating the need for traditional manufacturing methods like moulding or cutting. The ability to quickly and easily produce prototypes and functional parts has significantly reduced the time and cost involved in the design and development process. Moreover, 3D printing allows for greater design flexibility, as complex geometries and intricate details can be easily achieved. This has opened up new possibilities for product design, enabling manufacturers to create customized and personalized products on demand. As 3D printing technology continues to advance, it is expected to further disrupt traditional manufacturing methods and drive innovation in the industry.
Case Studies: Successful Incorporation of 3D Print Technology
One of the most compelling aspects of 3D printing technology is its proven success in various industries. Multiple case studies have demonstrated the seamless incorporation of 3D printing into product design and manufacturing processes. For instance, a leading automotive company utilized 3D printing to create intricate prototypes of new car models. This not only accelerated their development cycle but also allowed for more accurate testing and evaluation of design concepts. In the healthcare sector, 3D printing has been instrumental in creating personalized medical devices such as prosthetics and implants. This has significantly improved patient outcomes and accessibility to affordable healthcare solutions. Additionally, the aerospace industry has embraced 3D printing to produce lightweight components with complex geometries, leading to enhanced fuel efficiency and performance in aircraft. These case studies highlight the transformative impact of 3D printing in revolutionizing product design and manufacturing across a range of sectors.
Future Prospects for 3D Printing in Design and Manufacturing
The future prospects for 3D printing in design and manufacturing are extremely promising. As technology continues to improve and become more accessible, it is likely that 3D printing will revolutionize the way products are designed and manufactured. Its ability to quickly and cost-effectively produce complex and customized objects has the potential to greatly streamline the manufacturing process. Additionally, the ability to easily iterate designs and produce prototypes in a matter of hours or days rather than weeks or months can greatly accelerate the product development cycle. Furthermore, 3D printing has the potential to reduce waste and energy consumption compared to traditional manufacturing methods. With ongoing advancements in materials and printing techniques, it is clear that 3D printing will play an increasingly important role in the future of design and manufacturing.